MHB SERIES
The PCS MHB is designed for multi-process, high productivity plate processing with a large focus on machine rigidity and capability. The MHB comes standard with a state-of-the-art 3 digital axis CNC drill capable of high speed drilling, tapping, boring and countersinking. Optional configurations include flame cutting, plasma cutting, plasma & flame beveling, pipe cutting, ink jet printing, pin marking or any combination, all with precision motion control.
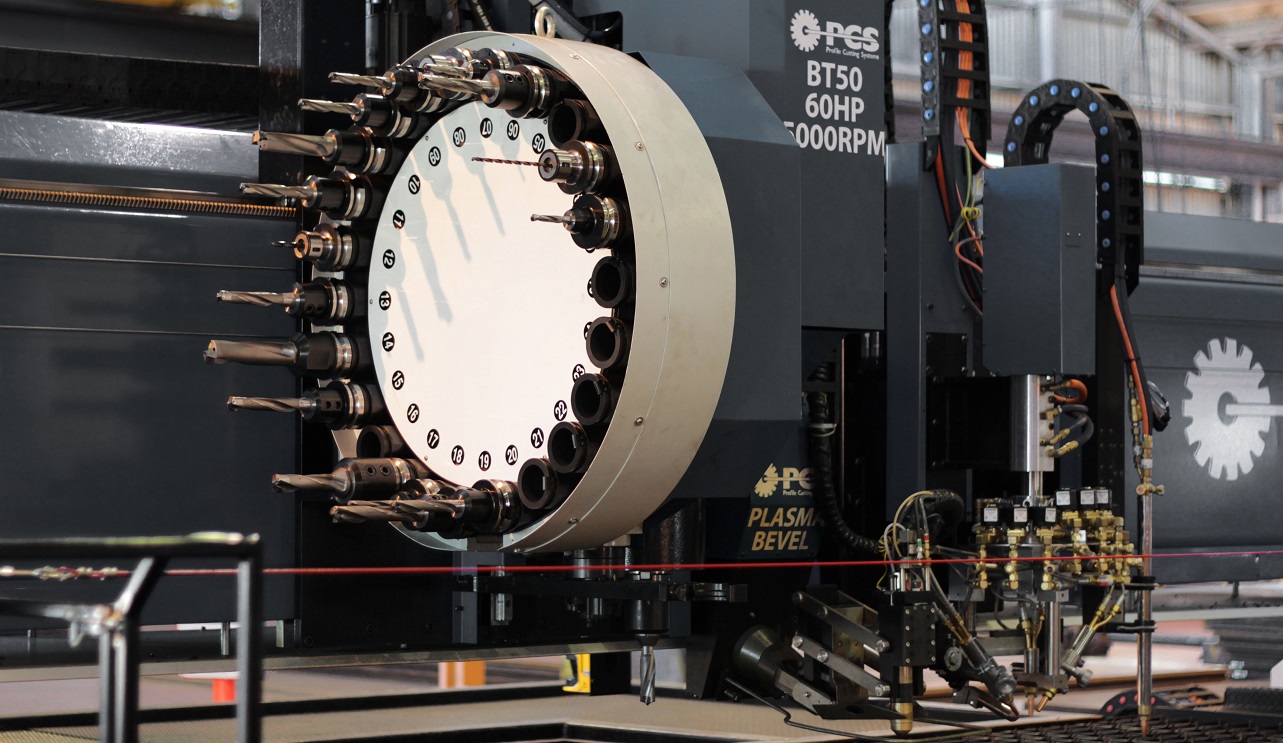
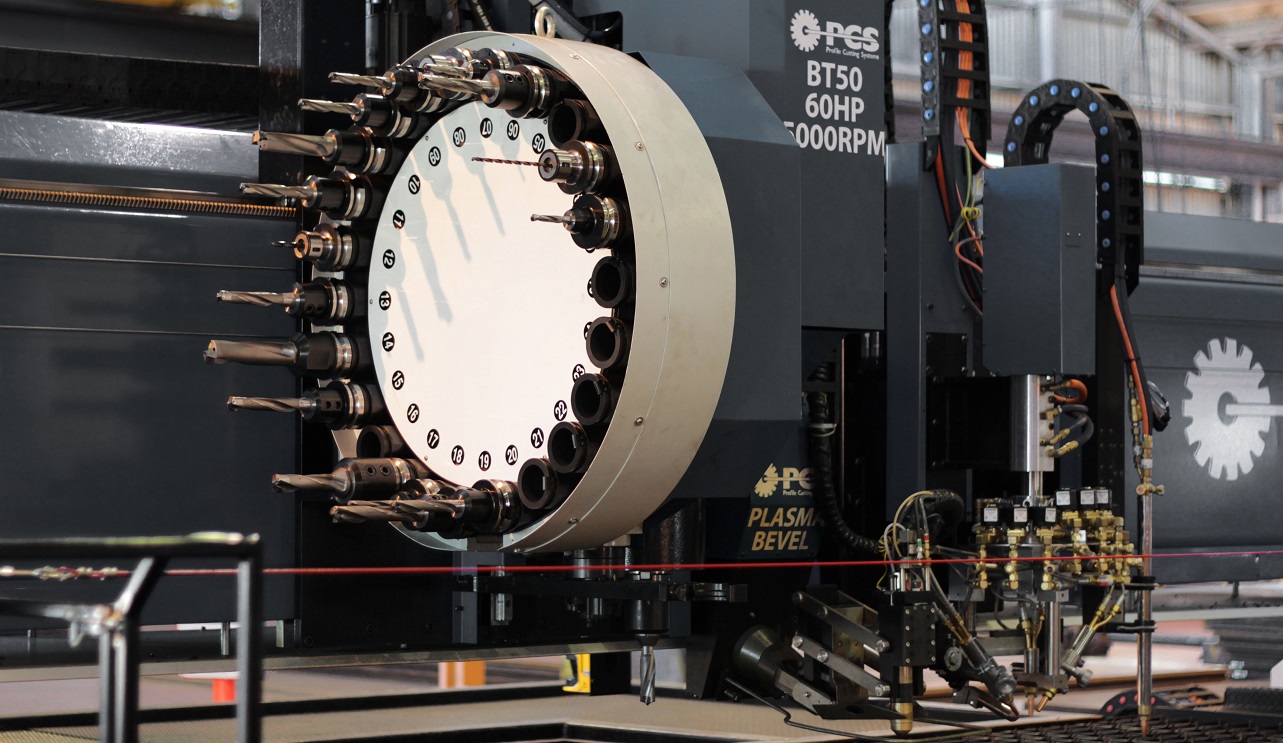
Features
- 30HP, BT-40, 5000rpm main spindle
- Drill up to 55mm holes (using HIGH SPEED tooling)
- Tap up to 35mm
- 24 tool Automatic Tool Changer (tool change time ~2.5sec)
- Through Tool Coolant. Flood coolant, Minimum Quantity Lubricant (MQL) or both
- Multiple Machining Operations – Drilling, Tapping, Milling, Counter boring, Counter sinking, Marking
- Multiple Cutting Operations – Plasma, Plasma Bevel, Flame, Flame Bevel
- Class Leading Burny 10 PC based CNC on custom PCS flat panel touch screen (up to 21.5”)
- Manufactured from non-proprietary components
- State-Of-The-Art Motion Control System – Bosch Rexroth digital drives and motors with absolute encoders
- Dual Ballscrew for servo driven feed and clamp
- Up to 1 ton of clamping downforce
- 20m/min traverse speed (limited)
- Ultra Heavy Duty floor mounted rail system made of machine hardened billet
- Automatic rail cleaning/polishing system. Cleans and polishes running surface as machine traverses
Key Features
- Hypertherm HPRXD Plasma
- Kaliburn Spirit II Plasma
- PCS Zero-Offset Plasma Bevel Head
- Oxyfuel cutting head
- PCS Triple Burner Oxyfuel Head
- Paint Jet Marking
- Pin Marking
Optional Heads
Machine Mass
The MHB main beam weighs in at over 4 metric tons. Large mass is crucial for high speed drilling. Unlike a standalone machining centre, plate profile machines such as the MHB are dynamic and process plate on a hollow cutting/drilling bed. This leads to what can be severe vibrations when drilling/machining. Therefore, the machine needs as much mass behind it as possible in order to minimise vibrations when drilling. Fewer vibrations means faster drilling and better tool life!
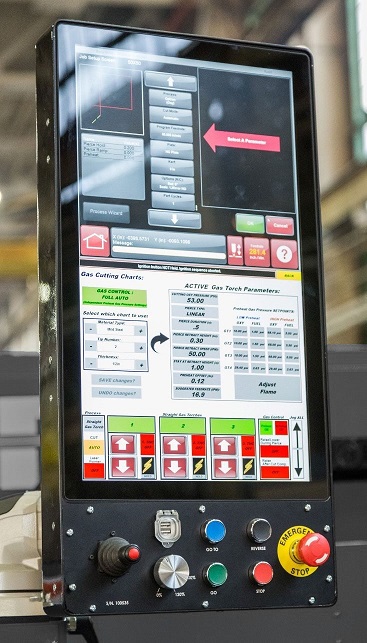
Solid Cutting/Drilling Table
The cutting/drilling table is as important as the machine on top of it. Our cutting/drilling tables are built just as tough as the MHB machine. They have several supports connecting the steel plate directly to the concrete floor. This is to minimize vibrations that are common with high speed drilling on profile machines.
Ease of Operation
Our state-of-the-art drilling HMI integrates seamlessly with the tried and trusted Burny 10 CNC. With pre-loaded drilling libraries, the operator doesn't require an in depth knowledge of drilling speeds and feeds. The HMI was designed to be extremely user friendly and as such can be mastered in literally seconds.
Productivity
High productivity is a crucial factor when investing in capital equipment such as profile cutting machines. The MHB achieves the highest productivity in its class thanks to its mass and a solid cutting/drilling table. The fastest drilling times and longest tool life are the key factors in achieving such high productivity.
Coolant System
We offer a Flood Coolant System, a UNIST Minimum Quantity Lubricant (MQL) system, external spindle jets or any combination on MHB series cutting and drilling machines.