BHB SERIES
The PCS BHB is the ultimate profile cutting machine. No other machine on the market offers a solution with as much emphasis on brute force, rigidity and capability. With options ranging from high speed drilling, tapping, boring, countersinking, beveling, gas and plasma cutting, pipe cutting, ink jet printing, pin marking, or any combination, all with precision motion control.
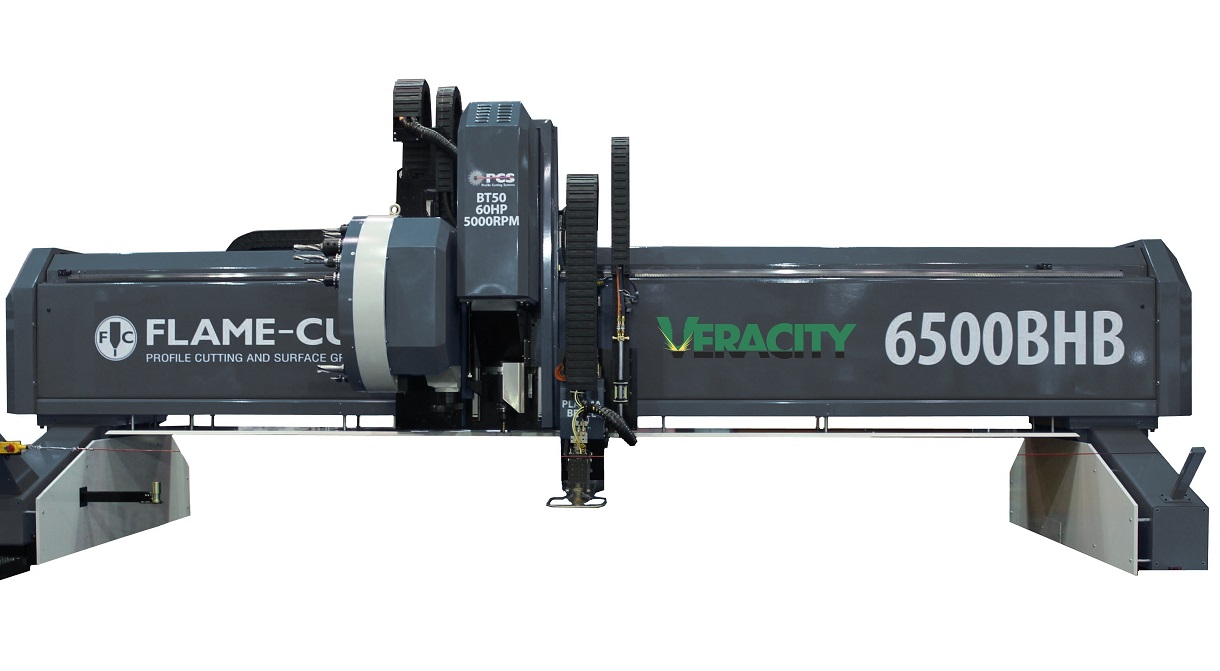
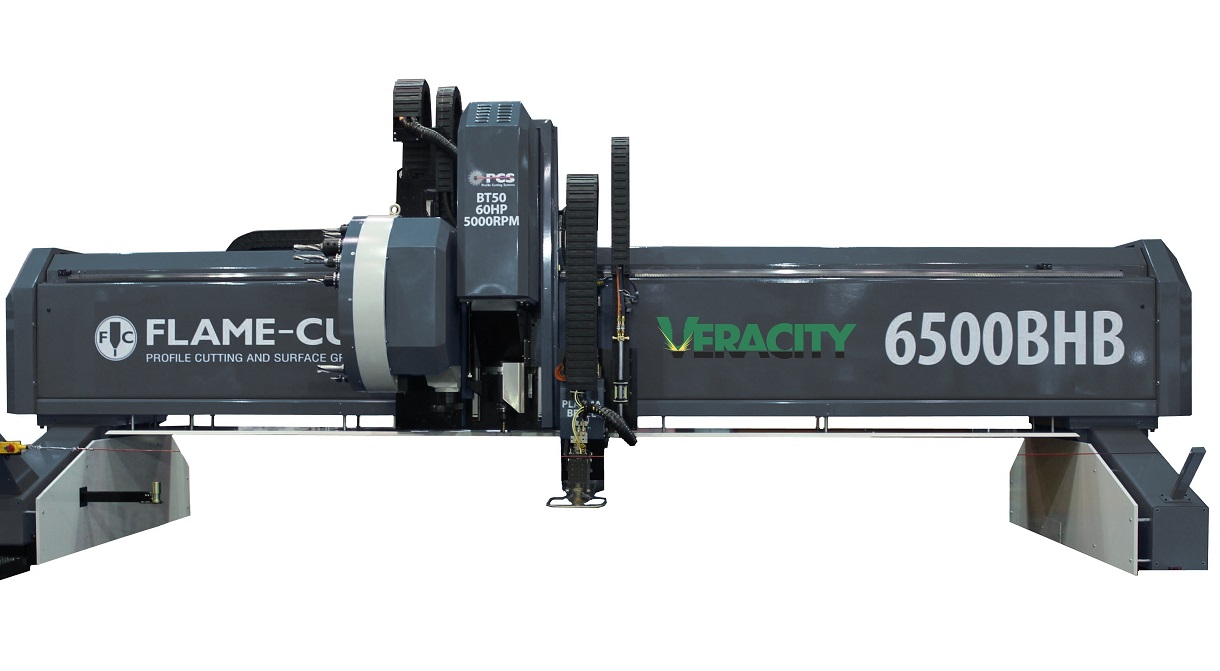
Features
Specifications
Features
Machine Design
The machine carriage is an all welded construction with a wholly
fabricated beam that utilizes several design characteristics used within
the aerospace industry. Supporting the fabricated beam are ultra solid
modular side supports. The drilling process is driven by a 60HP Digital
AC Servo motor. Connected to the motor is a BT50 or Cat50 spindle that
can handle up to 1395 FT/LB (1890NM) of torque. The drill assembly is
supported on linear rails with the vertical motion also driven by a Digital
AC Servo Motor. To ensure that the steel plate remains stationery the BHB
utilizes a fabricated clamping mechanism which is controlled by an additional
Digital AC Servo motor capable of producing up to 3.3 Ton (3.0 tonnes) of
force. To reduce machine downtime the BHB utilizes as standard a 24 Pot
Automatic Tool Changer which has a tool change time of 2.5 seconds.
To ensure ultra smooth operation the side supports run on extrareinforced
fabricated rails with a machined billet running surface
and vertically adjustable base plates which are adjusted on site to
provide a ridged and finely tweaked level running surface. With extra
powerful state of the art Digital AC dual drive system and integrated
active rail cleaning system, the PCS BHB will perform to the strictest
of tolerances for decades to come in a highly demanding industrial
environment. As several clients have already confirmed, if you are
looking to drastically reduce the lead time on projects that require
high speed drilling, cutting and plate edge preparation then the BHB
will provide results that cannot be matched. Furthermore one client
has stated that, "the PCS BHB has drastically reduced job completion
times, from 8 hours to only 2 hours."
- 60HP, BT-50, 5000rpm main spindle
- 24 tool automatic tool changer (tool change time ~2.5sec)
- Multiple machining operations – drilling, tapping, milling, counterboring, countersinking, marking
- Drilling capacity – 115mm, tapping capacity 38mm
- Multiple cutting operations – plasma, plasma bevel, oxyfuel, oxyfuel bevel
- Through tool coolant. Flood coolant, minimum quantity lubricant (MQL) or both
- Burny 10 PC based CNC on custom flat panel touch screen (up to 21.5")
- Manufactured from non-proprietary components
- State-of-the-art motion control system – Bosch Rexroth digital drives and motors with absolute encoders
- Dual ballscrew for servo driven feed and clamp with absolute encoders
- Up to 3 tons of clamping downforce
- 20m/min traverse speed (limited)
- Heavy duty floor mounted rail system made of machine hardened billet
- Automatic rail cleaning/polishing system. Cleans and polishes running surface as machine traverses
Key Features
- Customized cutting width
- Unlimited length
- On-Board Swarf extraction system
- Multiple gantries on common rail
- Plasma cutting
- PCS Zero Offset Plasma Bevel
- Independent torch station select
- Stud welding
- Steel Grate plasma cutting
- Rotary pipe cutting axis
- Flame (Oxyfuel) bevel
- Up to 10 flame (Oxyfuel) torches
- Extra hi-flow gas manifold
- Auto igniters
- Plate cooling rings
- Through tool MQL with high pressure air blast
- Through tool flood coolant
- PCS designed & manufactured wet or dry cutting tables
Customizations
- Paint marking
- Pin marking
- Powder marking
- PCS TurboGas - Automatic gas control for flame (Oxyfuel) cutting
- PCS IntuitiveGas - Automatic height control for flame (Oxyfuel) cutting
- On Table plate stock database
- Job reporting interface for managers
- Advanced maintenance logger
- Travelling dross bin
- Digitally zoned fume extraction
- Automatic plate alignment
- Automatic plate feed
- Extra safety devices
- Operators chair
- Operator safety shield
- Wireless pendant
- Hypertherm HPRXD Plasma
- Kaliburn Spirit II Plasma
- PCS Zero-Offset Plasma Bevel Head
- Oxyfuel cutting head
- PCS Triple Burner Oxyfuel Head
- Paint Jet Marking
- Pin Marking
Optional Heads
Machine Mass
Large mass is crucial for high speed drilling. Plate profile machines such as the BHB are dynamic and process plate on a hollow cutting/drilling bed. This leads to what can be severe vibrations when drilling/machining. Therefore, the machine needs as much mass behind it in to ensure that the kinetic energy is transferred only to the right places. Fewer vibrations means faster drilling and better tool life!
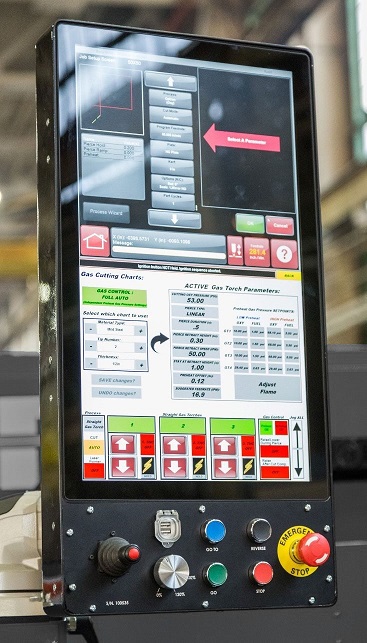
Solid Cutting/Drilling Table
The cutting/drilling table is as important as the machine on top of it. Our cutting/drilling tables are built just as tough as the BHB machine. They have several supports connecting the steel plate directly to the concrete floor. This is to minimize vibrations that are common with high speed drilling on profile machines.
Ease of Operation
Our state-of-the-art drilling HMI integrates seamlessly with the tried and trusted Burny 10 CNC. With pre-loaded drilling libraries, the operator doesn't require an in depth knowledge of drilling speeds and feeds. The HMI was designed to be extremely user friendly and as such can be mastered in literally seconds.
Productivity
High productivity is a crucial factor when investing in capital equipment such as profile cutting machines. The BHB achieves the highest productivity in its class thanks to its mass and a solid cutting/drilling table. The fastest drilling times and longest tool life are the key factors in achieving such high productivity.
Coolant System
We offer a dual minimum quantity lubricant and flood coolant system, unique only to BHB series cutting and drilling machines. Either coolant method (MQL or flood) can be selected for each individual tool in the on-board tool library. All BHB series machines using a UNIST MQL system utilise a specially made Dueblin rotary coupling to deliver the minimum quantity lubricant (MQL). Because the atomization point is as close to the cutting surface as possible, machines utilising this technology are able to achieve the best possible results with MQL. This equates to class leading drilling performance and tool life which is currently unmatched by any other machine on the market.
Specifications
Machine Dimensions | |
---|---|
Effective Cutting Width | Up to 27 ft |
Effective Cutting Length | Unlimited |
Overall Machine Height | 10 ft |
Machine Travel | |
---|---|
Traverse Speed | 800 ipm (20m/min) - Safety Limited |
Profiling Speed | Up to 800 ipm (20m/min) |
Max Acceleration | 3'/s/s (0.9 m/s/s) |
Machine Accuracy on Axis | 0.006"/3' (0.15mm/m) |
Machine Repeatability on Axis | 0.004" (0.1mm) |
Rack - Longitudinal Axis |
Helical Mod 3.0 Precision ground Rack has an accuracy of 0.0045"/3' (0.1mm/m) Material: S45C (C45) Steel |
Rail - Longitudinal Axis | 2 2/5" (60mm) machined hardened billet |
Rail/Rack - Transverse Axis |
1 2/5" (35mm) Rexroth precision ground linear roller rail and helical rack |
Rail - Drill Assembly | 1 2/5" (35mm) Rexroth Linear Roller Rail |
Pinions - Longitudinal Axis |
Helical Mod 3.0. Custom Precision ground Material: S45C (C45) Stee |
Pinions - Transverse Axis | Helical Mod 3.0. Rexroth Precision ground |
Pinion Thrust Bearings | As standard |
Cable Carrier |
Enclosed cable carrier standard Floor mounted |
Bearings |
Linear Roller bearings on transverse axis and drill assembly. High quality, readily available bearings used throughout. |
Integrated Active Rail Cleaning System | As standard |
Drive Amplifiers & Controller | |
---|---|
Controller |
Burny 10 LCD Plus with Custom PCS Apps 24" Glass touch screen, Windows 8 embedded, 4GB DDR3 RAM, 128GB SSD, SERCOS, remote diagnostics network ready |
Longitudinal & Transverse |
Independent 3-Axis (X, XX & Y) AC digital Rexroth IndraDrive amplifiers. SERCOS comms |
Main Spindle | 75HP (56kW) Digital Rexroth IndraDrive |
Plate Clamp | AC Digital Rexroth IndraDrive amplifiers |
Motors | |
---|---|
Longitudinal Axis |
32FT/LB (43.5Nm) max torque Bosch Rexroth AC servo motor |
Transverse Axis | 32FT/LB max torque Rexroth AC servo motor |
Main Spindle | 60HP Bosch Rexroth AC servo motor |
Spindle Lifter | 53FT/LB (70Nm) max torque Rexroth AC servo |
Plate Clamp | 53FT/LB (70Nm) max torque Rexroth AC servo |
Bevel Axis (optional) |
2x 1.2HP (0.90kW) AC, 1.3FT/LB (1.8Nm) max torque Rexroth servo motor 1x 2.5HP (1.86kW) AC, 6.0FT/LB (8.1Nm) max torqueRexroth servo motor |
Gearboxes | |
---|---|
Longitudinal Axis | Extra Heavy Duty Planetary Gearboxes <7 arcmin |
Transverse Axis | Planetary 16:1 Backlash <7 arcmin |
Main Spindle | Belt Reduction |
Spindle Lifter | Ballscrew, Belt Reduction |
Plate Clamp | Ballscrew, Belt Reduction |
Bevel Axis (optional) |
Planetary grease packed 1x 50:1 <9 arcmin 1x 5:1 <6 arcmin |
Standard Drilling Operation | |
---|---|
Spindle | Custom PCS 8" (200mm) diameter |
Max Spindle Load | 1395 ft/lb (1890 Nm) |
Max Clamping Thrust | 3.3 Ton |
Max RPM at Spindle | 5000 RPM |
Max Drilled Hole Diameter | 4 1/3" (110mm) |
Max Tool Diameter in Tool Changer |
4 1/3" (110mm), 5" (130mm) with adjacent pockets empty |
Max Stroke | 25 1/2" (650mm) |
Clearance Under Main Beam | 19 1/2" (500mm) |
Material Thickness | Up to 12" (300mm) |
Coolant System |
Through Tool Minimum Quantity Lubricant with High Pressure Air Blast - As Standard Through tool flood coolant - Optional |
Spindle Taper | BT50 or CAT50 |
Automatic Tool Changer | DETA 24 tool ATC – 2.5 sec tool change |
Drilling Time - 2" Hole, 4" Plate | ~ 26 seconds |
Recommended Plasma Cutting Operation | |
---|---|
Power Source | Kaliburn Spirit II Plasma System(s) |
Output Current | 100 - 400 amp |
Plasma Torch Lifter System | INOVA Torch Height Control System |
Cutting Capacity | .036" - 2" (1 - 50 mm) - Max capacity 3" (75mm) |
Standard Flame (Oxyfuel) Cutting Operation | |
---|---|
Number of Torches | Up to 10 |
Cutting Capacity | Up to 12" (300mm) |
Hi-speed Pre-heat | As standard |
Fast Pierce with Auto Retract | As standard |
Flame (Oxyfuel) Torch Lifter System | Soft PLC controlled as standard |
Standard Safety Features | |
---|---|
Machine Protection | Heat shields standard |
E-Stop | Independent Emergency-Stop Circuit |
End Limits |
Software controlled with redundant mechanical limit switches |